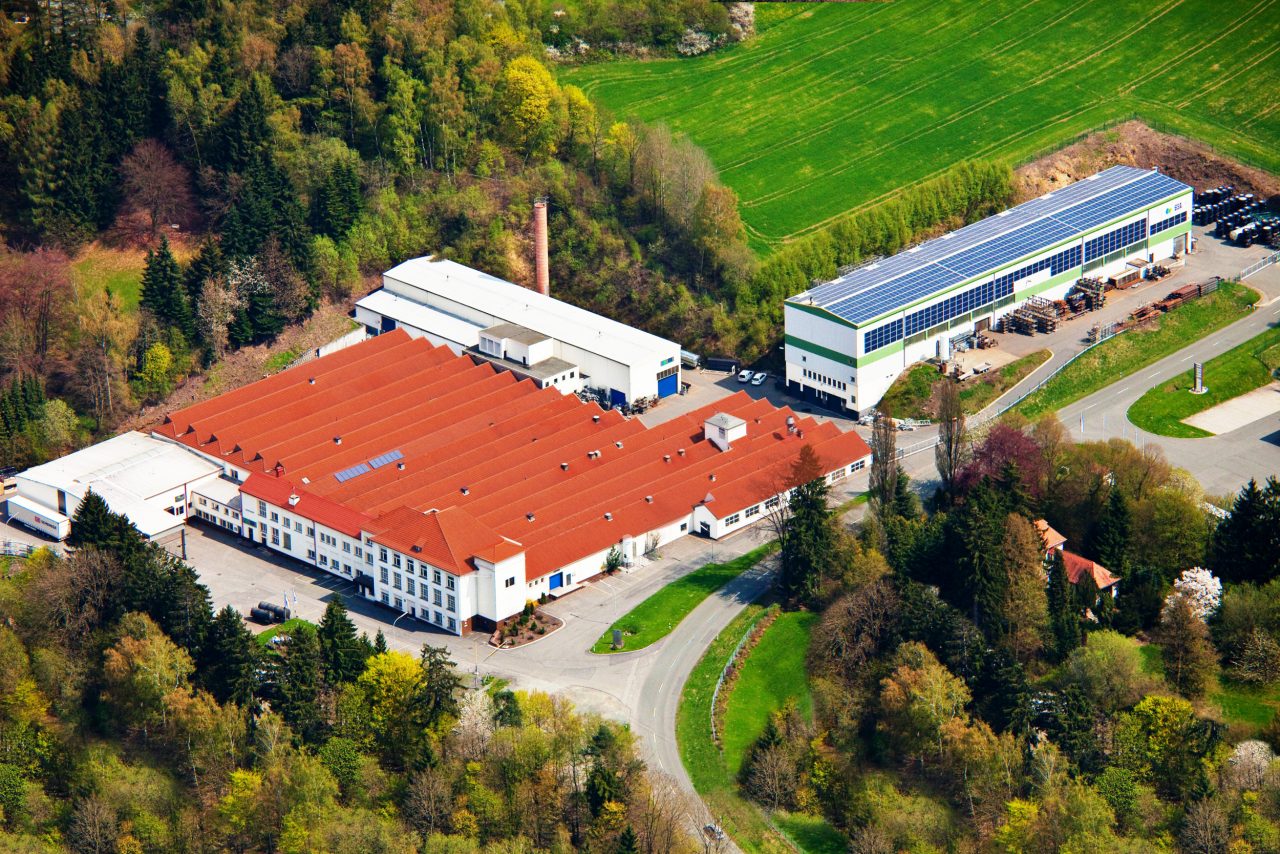
Efficiency is the most important design criterion for our FAN PRP reject presses. The structure – a combination of solid metal and replaceable components in the wearing area – is made of chemical-resistant stainless steel or robust steel for a high load capacity and a long lifespan. With a dead weight of about 7.4 tonnes and a length of just 4.1 metres, the largest model, the FAN-Beltec PRP 601, boasts an unbelievably compact and powerful design.
An intelligent control unit, combined with a frequency inverter and touch panel, allows access to all machine settings as well as automatic operation, including integration into an existing process control system. An additional local control system at the machine site optionally enables manual control of the main functions. For optimised operating costs, the wearing parts are easily replaceable and are available in various materials so that only the necessary quality level need be used. The machines are easily accessible from both sides by opening the service flaps.
FAN PRP reject presses have a self-supporting screw that is divided into drive and press zones combined with a specially developed gearbox and a powerful, efficient electric drive. The compressed solids, typically rejects from paper recycling at cardboard and paper plants, exit the machine horizontally in the discharge direction. Two symmetrical press flaps, controlled by the control system, ensure optimal back pressure. This design prevents blockages and enables optimal values with regard to dry matter content and volume reduction.
Model | Capacity (T/H) | Inlet consistency (%DM) | Max. particle size in mm | Dry matter content* | Volume reduction | Installed power (KW) |
---|---|---|---|---|---|---|
FAN PRP 426 | 0.3-0.8 | 12-20 | 100 | Bis zu 70% TS | 50-75 % | 22+2.2 |
FAN PRP 601 | 0.5-2.5 | 12-20 | 190 | Bis zu 80% TS | 50-75 % | 37+2.2 |