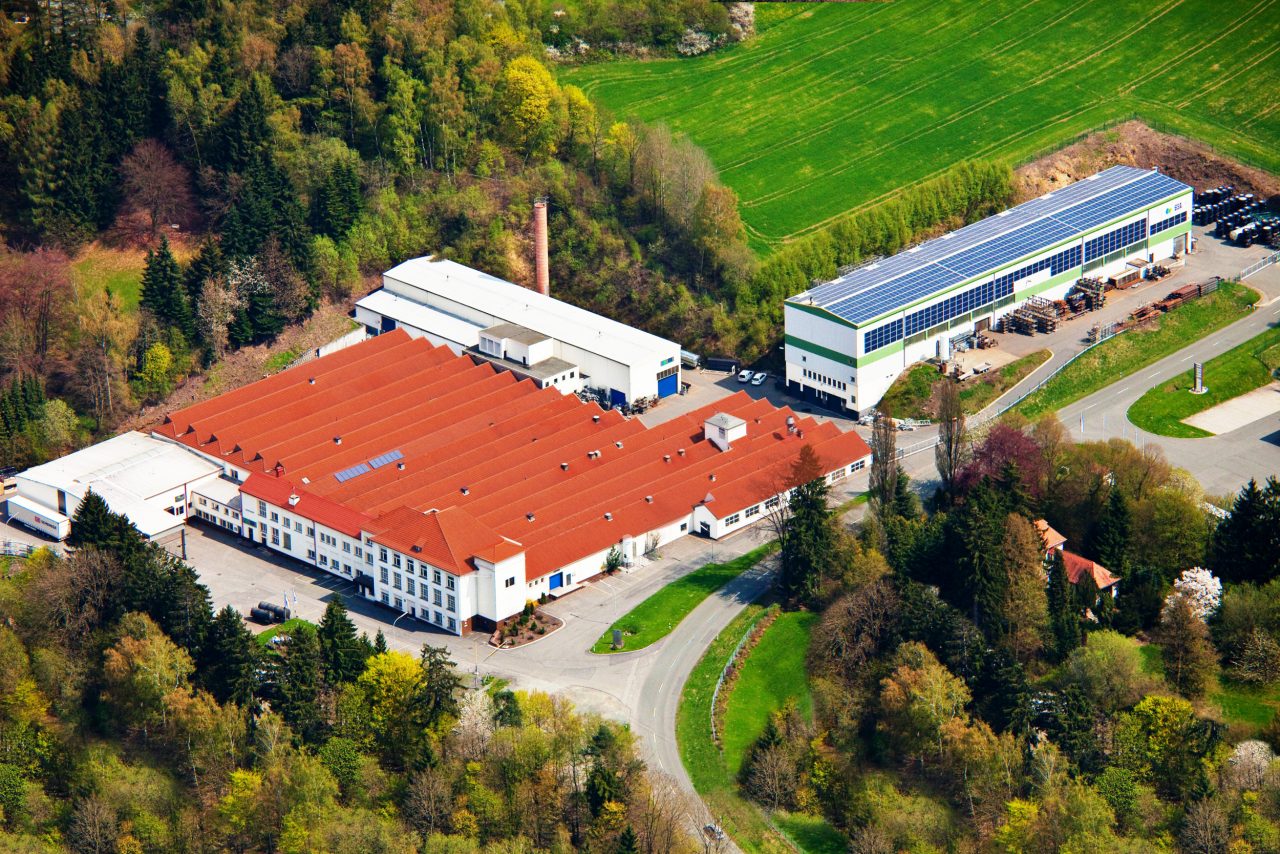
The sludge press SPS 1200 is used in municipal water treatment plants as well as anywhere industrial sludge must be dewatered, such as in the meat processing, dairy or leather processing industries. With the sludge press system, FAN has rounded out its portfolio of pump technology for professional separation, making it a full service provider on the market for sludge dewatering.
The FAN sludge separator SPS 1200 has a drive output of 0.55 kW and is able to produce solids with a dry matter content of up to 30%. The main area of application for this sludge separator lies in municipal water treatment plants, which currently often make use of decanter centrifuges. The goal of the new sludge separator is to continuously extract liquid from sludge to reduce the moisture level and the volume. The more effectively sewage sludge can be dewatered, the lower the disposal and transport costs.
The geometry of the screw is specially adapted for sludge separation and produces a slow, uniform pressure build-up in the machine.
This results in pressed-out water of high quality while at the same time achieving a high dry matter content in the solid.
By using high-precision stainless steel wedgewire screens, a larger open area per square metre of screen surface is achieved than with perforated screens, resulting in a higher throughput.
Compared to other screw presses, the FAN sludge press separator has a higher specific throughput capacity per m² of screen area. As a result, this comparatively small machine achieves the same performance as much larger separators from competitors.
The patent-pending screen washing device automatically cleans the screens at adjustable intervals, washing the entire screen surface evenly.
Thanks to the compact design, inspection and maintenance work is much easier to carry out compared to large presses having the same capacity. Maintenance costs per year are many times lower than for decanter centrifuges or belt presses.
Compared to other screw presses, the FAN sludge press separator has a higher specific throughput capacity per m² of screen area. As a result, this comparatively small machine achieves the same performance as much larger presses from competitors.